High Speed Mechanical Testing and Imaging: Digital Image Correlation
High Speed Testing, Analysis and Imaging of Materials
Shimadzu’s HPV-X2 Ultra-high Speed camera provides frame rates up to 10 million frames per second with state-of-the-art light sensitivity. It is known by scientists globally as the camera of choice for advanced impact studies and fluid mechanical investigations. It is the preferred camera for Digital Image Correlation studies of ultra-high-speed mechanical phenomena. Shimadzu’s high speed, hydraulically controlled HITS machines provides tensile or impact testing at controlled rates up to 20m/sec. Combined with 2 HPV-X2 cameras, HITS machines are ideal for 3D DIC studies of advanced materials. Scientists worldwide depend on Shimadzu HITS systems to assist in computer modeling of new materials.
Hyper Vision HPV-X2 Ultra-High-Speed Video Camera
Ultra-High-Speed Video Recording of Up to 10 Million FPS
- Recording speed of 10 million frames/second, the highest in its class
- Larger, clearer, high-sensitivity recording
- Equipped with synchronized recording function, and high-level analytical capabilities that accommodate a variety of software programs
- ISO 16,000 - 6 times higher sensitivity compared to conventional cameras
Featured Applications
Ultra-High-Speed Aerospace Applications
In the development of aerospace materials, ultra-high-speed cameras are used to investigate the failure behavior of materials caused by high-speed flying objects, and the deformation and failure behavior of materials caused by high-speed impacts. In addition, ultra-high-speed cameras are utilized for the development of thrust generators, aerodynamic design via wind tunnel tests, the observation of damage in lightning strike tests, and basic research into shockwaves, detonation waves, and other high-speed wave motion phenomena.
Ultra-High-Speed Automotive Applications
In order to develop high-output, high-efficiency automobile engines, detailed observations and analyses of the structural components of the engine are required. This includes the process of fuel injection by fuel injection equipment (injectors), and the process of fuel ignition by spark plugs. In addition, the development of automobile bodies utilizing new materials such as lightweight and very strong carbon fiber reinforced plastics (CFRP) is actively being pursued. However, in developing such new materials, it is necessary to observe and analyze the deformation and failure behavior of materials when they undergo an impact. In recent years, the deformation behavior of materials recorded using ultra-high-speed cameras has been analyzed using image analysis software.
High-Speed Imaging of Hypervelocity Microparticle Impact −Development of Laser-Induced Particle Impact Test−
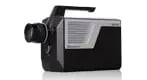
This article describes how a high-speed video camera was used to image the high-speed flight and collision of microparticles. First, impact experiments were conducted on polymer materials using various kinds of particles to investigate the shape of impact marks using LIPIT. Then nanoscale analysis was performed on high-speed collision phenomena using the coarse-grained molecular dynamics method and discussed the mechanism of plastic deformation behavior from the viewpoint of molecular chain deformation.
High Speed Tensile Test of High-Strength Steel
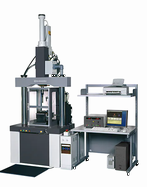
High-strength steels (HSS) provide better mechanical properties than conventional structural steels and are widely employed in the automotive field. In fact, HSS high specific strength (tensile strength divided by density) plays a key role in the weight reduction of car parts, greatly contributing to the reduction of CO2 emissions. One of the basic mechanical properties of the materials is the tensile strength, and can be measured with a conventional static tensile test (low speed). However, since the tensile strength of HSS increases with the strain rate1)2), the tensile strength value obtained with a static test might not be suitable for an accurate component design. For such reason, in order to guarantee a safe and efficient design of automobile parts that may undergo impacts (high speed loads), high speed tests must be conducted to investigate the relationship between the material tensile strength and the strain rate. In this work, the tensile strength-strain rate relationship has been evaluated with tensile tests at a speed ranging from 0.0001 m/s to 5 m/s. Grip teeth featuring a pin allowed to conduct the tests without slippage. The results showed that tensile strength at high speed is 10% higher than the one measured at low speed.
High-Speed Tensile Test of CNF-Reinforced Plastic
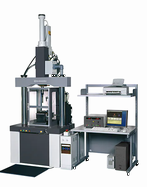
Cellulose is the main component of plants. It is also the most abundant carbohydrate on earth and has been used as raw materials of paper and textiles since antiquity. In recent years, cellulose nanofiber (CNF) with higher functionality realized by defibrating cellulose to the nano level has attracted considerable attention. CNF has low environmental impacts, as it is a plant-derived material, and possesses a variety of desirable functions, including low linear expansion, a gas barrier property, and transparency. It is also lightweight, weighing only 1/5 as much as steel, and displays high specific strength 5 to 8 times stronger than ferrous materials. It is essential to clarify not only the static echanical properties of materials, but also their impact properties, fatigue characteristics, and thermal characteristics. In this article, the tensile strength of CNF-reinforced plastic was evaluated at various test speeds (strain rates) by using a Shimadzu testing machine and high-speed impact testing machine. The fracture surfaces of the specimens after the tests were also observed by using an electron probe microanalyzer (EPMA).
Development of a holistic approach for force and strain measurements in high-speed tensile tests
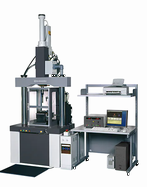
Comparison and dependency of HITS-T10 system integrated and additional techniques for measuring test forces and stresses, displacements and strains. Innovative measurement with HPV-X2 camera and DIC-analysis, with which true test stresses and strains can be calculated.
Fracture Observation of Glass in Ring-on-Ring Bending Test
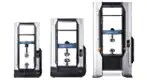
In this experiment, the fracture behavior of strengthened glass in a ring-on-ring bending test was observed using a Shimadzu Hyper Vision HPV™ -X2 high-speed video camera. The HPV-X2 has a recording speed of maximum 10 million frames per second (10 Mfps), which not only made it possible to clearly observe the point of origin of the fracture, but also the detailed condition of crack propagation.
Fracture Observation and Observation of Strain Distribution of Plastic Material with Hole in Impact Compression Test
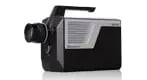
This article introduces an example of observation of the fracture behavior of an acrylic block having a round hole in its center in an impact compression test using the Hopkinson bar method. In addition, a random pattern was made on the surface of the specimen, and the strain distribution on the surface was visualized by DIC analysis.
Continuous Visualization of Process of Positive Streamer Initiation, Propagation, Spark, and Bubble Expansion in Water
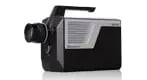
Contrary to the previous assumption that the materials do not fail under fatigue if the applied stress is below the so-called fatigue limit; with the availability of the novel very high cycle fatigue (VHCF) testing techniques, it has been found that materials do fail under fatigue loading even when the stresses are below the conventional fatigue limit, suggesting the nonexistence of such a limit. Some alloys of both lattice types (bcc and fcc) show a change in crack initiation site from surface to subsurface in a region from HCF to VHCF.
HITS-X Series High Speed Impact Testing Machines
To reduce weight and thereby improve fuel economy, aerospace and automotive designers are increasingly utilizing light-weight plastics and new composite materials.
To aid in the adoption of these new materials, designers are employing Computer Aided Engineering (CAE) modeling methods to reduce the costs associated with prototype production.
Thorough mechanical characterization of new plastics and composites is essential to ensure effective modeling and the safe adoption of these new materials in final products. Particularly important for modeling accuracy is reliable input data concerning materials’ mechanical behavior at different strain rates and temperatures.
The Shimadzu HITS-X Series instruments allow the study of materials tensile and puncture behavior at testing speeds ranging from 0.0001 to 20 meters per second at temperatures ranging from -40 to 150 C.
Visualization of Progress of Internal Damage in Carbon Fiber Composite Materials and Mechanism of Impact Strength
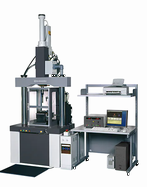
Fiber reinforced plastics (FRP) have higher mechanical properties per unit weight than metal materials such as steel and aluminum and therefore are used now as substitute materials for metals in a variety of industrial products. Particularly in recent years, high quality carbon fibers, resin-impregnated prepregs containing those fibers, and advanced molding technologies have been developed. As a result, FRP has now gained wide acceptance and has an extensive record of actual use, and is also beginning to be used in main structural parts of aircraft and automobiles, in which high reliability is essential. However, in the case of carbon fiber reinforced plastic (CFRP), which consists of carbon fiber and resin, in combination with the existence of adhesive interfaces, the failure process also has an extremely complex mechanism.