Additive Manufacturing (3D Printing)
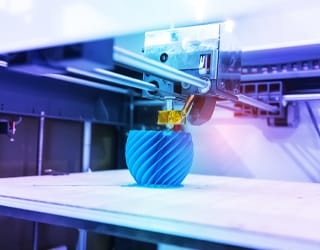
Testing, Analysis and Inspection of 3D Printed Materials
Additive manufacturing (3D Printing) techniques are revolutionizing the design and fabrication of objects as varied as aircraft engine parts, automobile components, orthopedic and dental implants, clothes, foot ware and foods. Additive manufacturing processes include: Binder Jetting, Directed Energy Deposition, Material Extrusion, Material Jetting, Powder Bed Fusion, Sheet Lamination and Vat Photopolymerization.
Shimadzu instruments are used worldwide to characterize the composition of raw materials used in additive manufacturing and the mechanical behavior of finished 3D printed materials.
Below are links to recent publications and application notes.
Featured Applications
Ultrasonic Fatigue Testing for Additively Manufactured Metal Alloys
Compared with traditional fatigue testing, the ultrasonic method achieves much speedier results along with the ability to run extremely high test cycles in a reasonable time frame.
Used with permission. ©ASM International.
Thermal Properties of Composite Filaments for 3D Printers
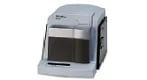
Because 3D printers utilize the characteristic that the filament material softens when heated and then hardens when cooled, the differential scanning calorimeter (DSC), which enables detailed analysis of fusion and crystallization, is extremely effective in material selection and setting of the molding conditions. This article introduces an example in which the thermal properties of several composite filaments for 3D printers were measured with Shimadzu thermal analyzers.
Very High Cycle Fatigue (VHCF) Assessment of Laser Additive Manufactured (LAM) AlSi12 Alloy
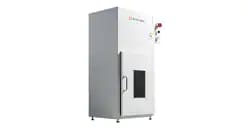
Contrary to the previous assumption that the materials do not fail under fatigue if the applied stress is below the so-called fatigue limit; with the availability of the novel very high cycle fatigue (VHCF) testing techniques, it has been found that materials do fail under fatigue loading even when the stresses are below the conventional fatigue limit, suggesting the nonexistence of such a limit. Some alloys of both lattice types (bcc and fcc) show a change in crack initiation site from surface to subsurface in a region from HCF to VHCF.
Metal Powders used for Additive Manufacturing measured with SALD-2300 and MS-23
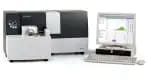
Before measuring life time properties it is also important to measure the particle size distribution from the additive material, this can be measured with SALD-2300. Measurements in a range from 17 nm up to 2500 µm. With the rise of metal powder-based additive manufacturing and its acceptance for critical applications, it has become important to understand the behavior of the raw materials used in different AM Techniques.
Viscosity Evaluation of Cellulose Nanofiber-Reinforced Composite
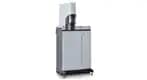
Poor conditions can cause molding defects including short shot (underfilling), overcharge, sink mark, and voids. Moreover, even if molding is performed under the proper conditions, changes in the condition of the raw material resin can lead to molding defects. Thus, it is essential to determine the optimum molding conditions for CNF reinforced composite materials. As one technique for evaluating these moldability properties of thermoplastic resins, in this study, fluidity was evaluated by using a Shimadzu CFT-EX flowtester.