Identification of Composite Material Failure Mechanisms —Observation of the CFRTP Failure Process—
Carbon fiber reinforced thermoplastic (CFRTP) composites, which exhibit excellent processing, mass production, and recycling properties, are expected to replace conventional materials, such as metals, in general-purpose transport vehicles, especially mass-produced vehicles. However, the internal failure mechanisms that occur during the deformation process in CFRTP composites are not sufficiently understood in terms of properties such as static strength and fatigue strength. Here, we introduce a combined system that enables observation of a load applied to a test sample and internal damage within the sample when the load is applied, key indicators for determining the failure mechanisms of CFRTP composites.
Fatigue Tests within an X-Ray CT System
Fatigue Test on Aluminum Test Sample and Observation of Crack Extension
CT imaging can be performed while the test sample is mounted on a fatigue testing machine (air servo).
• During CT imaging, the test is temporarily paused.
Tensile and Compression Tests within X-Ray CT System
-
- Tensile Testing Machine
-
Tensile Test Results for Felt
It can be seen that after applying tension, the fiber orientation in the felt is mainly 0 degrees, the tensile direction.
Three-Point Bending Test + Stress Measurement within an X-Ray CT System
Three-Point Bending Test of a CFRTP and Observation of Its Internal Structure
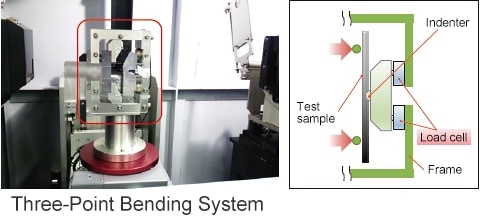
The internal damage within the test sample can be observed while obtaining the stroke and stress graphs.
This research was performed as part of the Japanese Ministry of Economy, Trade and Industry—NEDO sponsored project “Research and Development of Innovative Structural Materials.”
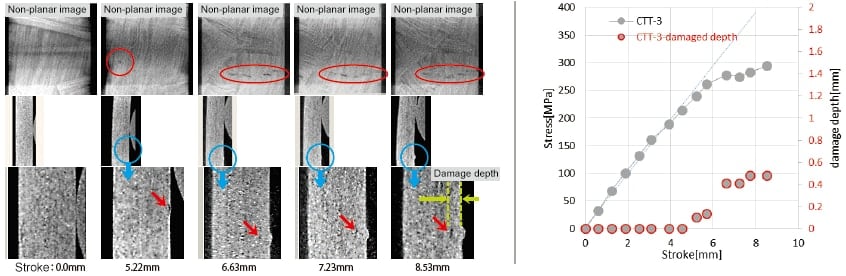
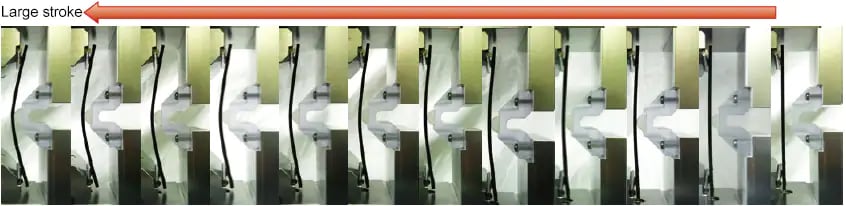
- Combined system produced by a manufacturer that specializes in X-ray CT systems and testing machines.
- Enables the change of stress applied to the test sample and the progress of internal damage to be observed, which was previously difficult.